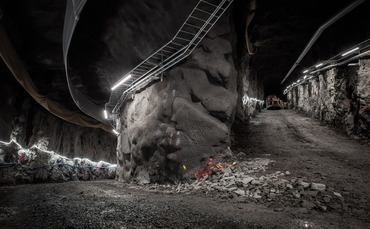
A Swedish pilot project has found that adding hydrogen storage capacity to the green gas’ production process could cut costs by between 25 and 40 per cent.
Launched in 2016 as a collaboration between from steel manufacturer SSAB, mining firm LKAB, and energy giant Vattenfall the Hybrit project aims to create a fossil fuel-free value chain capable of delivering zero emission steel at scale.
The project recently concluded a month-long commercial test of a hydrogen storage site adjacent to Hybrit’s pilot plant for producing fossil-free iron in Luleå, finding that adding storage capacity significantly reduced the variable cost associated with hydrogen production.
According to an update from Vattenfall, the aim of the test was to produce green hydrogen by water electrolysis using clean electricity that was sourced at the lowest possible cost – for example, during parts of the day when renewables generation was in good supply.
It then harnessed a lined cavern technology in a facility brought on stream 30 metres below ground during summer 2022. Measuring 100 cubic metres and storing hydrogen pressurised up to 250 bar, it is estimated that 100,000 to 120,000 cubic metres of stored hydrogen would be sufficient to power full-size steel mill production for up to four days.
Marie Anheden, senior project manager at Hybrit, said despite the fact that Vattenfall optimised trading and operations against real electricity prices during a period with low price variations, the test results were “very good”, confirming that access to storage capacity could significantly reduce the cost of hydrogen production.
“The tests were conducted in a close collaboration between Hybrit Development and Vattenfall,” she said. “By applying it in actual circumstances, we were able to follow in real time how much money was saved by using what was stored.
Mikael Nordlander, head of industry decarbonisation at Vattenfall, added that the results were “exciting and important” given the significance of green hydrogen in enabling the decarbonisation of the steel industry.
“Large-scale hydrogen storage makes it possible to adapt electricity consumption in a system of varying availability and prices and at the same time can supply the industry with hydrogen more stably and cost effectively,” he said.
“Used on a large scale, hydrogen storage can have a dampening effect on electricity price variations, which would favour investments in new electricity generation from all forms of fossil-free power.”
Stefan Savonen, senior vice-president for energy and climate at LKAB, said the results were particularly significant given the mining firm aims to eventually change its entire iron ore product production to fossil-free iron sponge produced using hydrogen gas.
“We will need to produce over one million tonnes of hydrogen and consume over 70 TWh of fossil-free electricity per year when we have restructured the entire operation by 2050,” he said. “Reducing costs is therefore absolutely necessary.”
Vattenfall, SSAB, and LKAB have invested SEK200m – or around £15m – in Hybrit, alongside just over SEK52m from the Swedish Energy Agency.
Its claimed that the project, which produced the world’s first fossil-free steel in August 2021, could single-handedly cut Sweden’s carbon dioxide emissions by 10 per cent and Finland’s by seven per cent.
Keep up to date with all the latest green business news by signing up to the free Daily and Weekly BusinessGreen Newsletters.